Hopping happy — alumnus Sam Glasgow is having a field day with resurrected hops industry
Ankle-deep in gummy mud for a photo shoot for the UFV Skookum magazine, Sam Glasgow can’t help but smile.
His Cascades are cresting. Chinook fight through rich, black soil. Hops are back — and Glasgow’s leading the way.
“I like producing food that people enjoy,” he says, firmly planted between rows of early spring hops. “And these days, especially, it’s pretty easy to see people love their beer.”
Hop fields are sprouting across the valley and reclaiming land once thick with pickers and poles, thanks to people like Glasgow, a 2014 UFV Agriculture grad turned field manager for Abbotsford’s Valley Hops Ltd.
“We’re taking care of people who want to produce income with their land. Hops have been around for a long time here, but a new chapter is definitely firing up.”
B.C.’s hop industry took root in the 1890s, growing quickly when the 1924 draining of Sumas Lake exposed a swath of fertile farmland. The industry’s high-water mark topped in the 1940s with nearly 4,000 people employed through harvest season.
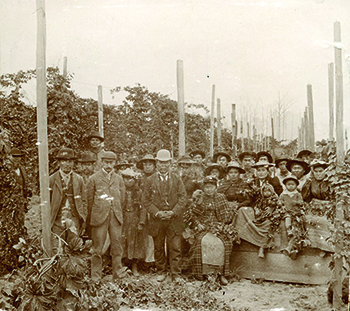
“Everyone seems to have a grandparent or two who used to work in the hop fields,” Glasgow says. “It’s hard to imagine today just how big it was here. They say the air was thick with the hops smell every harvest.”
Friendships and families started in those fields — many now covered by pharmacies and coffee franchises. Pickers lived among the fast-growing plants, setting up small communities, building bath houses and playing cards. Picking was an important economic activity for Indigenous people, including local Stó:lo, as well as Mennonites and other ethnic groups. Sometimes entire families picked together.
That work scaled back in the ’50s when picking machines arrived that could harvest more in one day than hundreds of hired hands.
Chilliwack’s hop industry dried up after Fred Haas, whose John I. Haas Hops Company had acquired all 1,325 acres of hops fields, willed them to Georgetown University in the 1990s.
It didn’t take long for that land to be sold — snapped up by local buyers to satisfy tastes for cattle, corn, and shopping centres.
The recent hops resurrection is fuelled by a craft beer boom that drove the number of B.C. breweries to about 120 in 2016 from only 50 a few years earlier (an increase of 240%). Rising demand and challenging climate issues created concerns for a global hops shortage in 2016.
People like Glasgow are taking action to meet the increased demand.
Valley Hops manages partner-farmer fields, recommending what varieties to plant, providing input on a variety of agricultural areas including irrigation design, field and crop health management, and harvest techniques. At harvest time, Valley Hops drives the cut bines over to a sister company — BC Hop Co. — and feeds plants into a German-made Wolf harvester. The size of a small ship, the harvester sends hop cones into an equally large beast of a drying machine.
Dried to a specific humidity, the hops eventually draw into bags shaped like hay bales that are hand-sewn shut and sent for pelletizing. They’ll be pressed into the shape of rabbit pellets, packaged tightly with a blast of CO2, and launched into the hands of eager brewers.
The total land in B.C. covered by hop farms won’t be known until 2016 Agricultural census numbers are released, but Glasgow says Valley Hops alone will manage 120 acres in 2017, up from 50 the year before.
“It takes a lot of work and resources,” he says. “Hops are pigs for water. They want it running past their roots and drink it all day, but don’t want to sit in a puddle. They’re kind of picky, I guess.”
Another major local hop provider is Chilliwack Hop Farms, while some independent growers like Chris Sartori continue the tradition of working their family farms. His daughter, UFV women’s basketball standout Kayli Sartori, is an Agriculture student studying with an eye on the hop industry.
Glasgow started studying at UFV with plans to be an English major, but lost interest in his original goal of teaching. Having worked in blueberry fields as a teenager, he changed paths. “Education is important, but feeding people is also really important,” he says.
“You’ve got to be able to live before you can learn, so I switched over to Agriculture. UFV’s program was touted as one of the more hands-on programs. It was close to home, which was nice. I could keep a job and go to school so I didn’t fall into any debt issues. I also learned how connected the instructors were with industry professionals. And now that I’m in the industry, it’s even more obvious.”
Needing a theoretical business plan to complete one of the courses in the program, Glasgow considered his own interests.
“Like many university students, I liked to drink beer,” he recalls.
“And I didn’t want to do the typical blueberry thing, so I developed a 10-acre hop farm plan.”
While at UFV, Glasgow worked as a tree planter and research assistant with the provincial Ministry of Agriculture. After graduating and a short stint selling nursery pots to greenhouses, he headed back to hops, becoming a founding board member of the BC Hop Growers Association, a non-profit association supporting hop farmers and bringing industry issues to government attention.
When he started growing, the bulk of hop production was taking place in Washington State, but even small variations in climate meant Fraser Valley fields demanded special attention.
“We can’t just be dumping nitrogen into the soil trying to get their production numbers, we need to think things through.”
Glasgow’s UFV instructors left a lasting impression: don’t memorize information that changes.
“The most important thing I learned from the instructors at UFV was to be an autodidact [self-taught, lifelong learner]. How to learn, how to search, how to be skeptical, how to keep working to get the answers you need.”
Glasgow wants to be a big part of B.C.’s hop future, and already has plans to incorporate some tree planting and fruit harvesting practices into his fields.
“We need to make sure our product meets the high standards breweries have come to expect. A lot of people count on hop producers and, at the end of the day, that’s what I’m looking for,” he says. Another smile sneaks through his thick copper beard.
“Well … that and maybe a beer.”
Other alumni also involved in the microbrew revival
From biology to brewing, Nick Fengler’s hop odyssey is anything but ordinary. After graduating from UFV in 2010 with major in Biology and minor in Chemistry, Fengler worked as a field biologist, conducting bird counts and providing environmental consulting.
“I remember standing in the Tsawwassen flats up to my knees in mud at 5 am in the cold rain counting bird poo and thinking ‘Ahh, this is not right for me.’”
At the urging of friends who homebrewed, Fengler sent letters asking if breweries could put his science degree to work. Aldergrove’s Dead Frog answered yes, but
said he would have to start at the bottom. Within two years he rocketed from keg washer to head brewer.
Now he is head brewer at Chilliwack’s Old Yale Br where he uses hundreds of pounds of Sam Glasgow-grown hops and sees a steady stream of his former UFV professors and classmates.
“I enjoyed UFV and I’m really glad it helped lead me here. Brewing’s very satisfying, a lot of room for creativity. It’s a blend of my science and technical background, but also gives me this creative outlet — best of both worlds, really.”
Homebrew hobbyists fuel demand for hops
UFV alumni Simon Dalton (BA ’05) and Brandon Kelley (BBA ’07) have homebrewed for about three years, using local hops in 5-gallon batches with styles ranging from German lagers to Belgian sours and wildly hoppy west coast IPAs.
Both are members of the Ten Corners Homebrew Club, which rotates monthly meetings between Chilliwack and Abbotsford.
“I love making something from scratch,” Dalton says while helping brew an ale in Kelley’s east Abbotsford garage.
“There’s satisfaction when you and your friends can enjoy something you made yourself.”
Kelley, a chartered professional accountant who served as treasurer for the Abbotsford Chamber of Commerce, agrees. He built his own beer tap system out of spare wood and an old freezer.
“I like having a hobby I can drink,” he says.
“It’s usually great beer and cheaper than buying commercially. Hard to beat that.”
Originally published in the 2017 edition of UFV Skookum magazine.